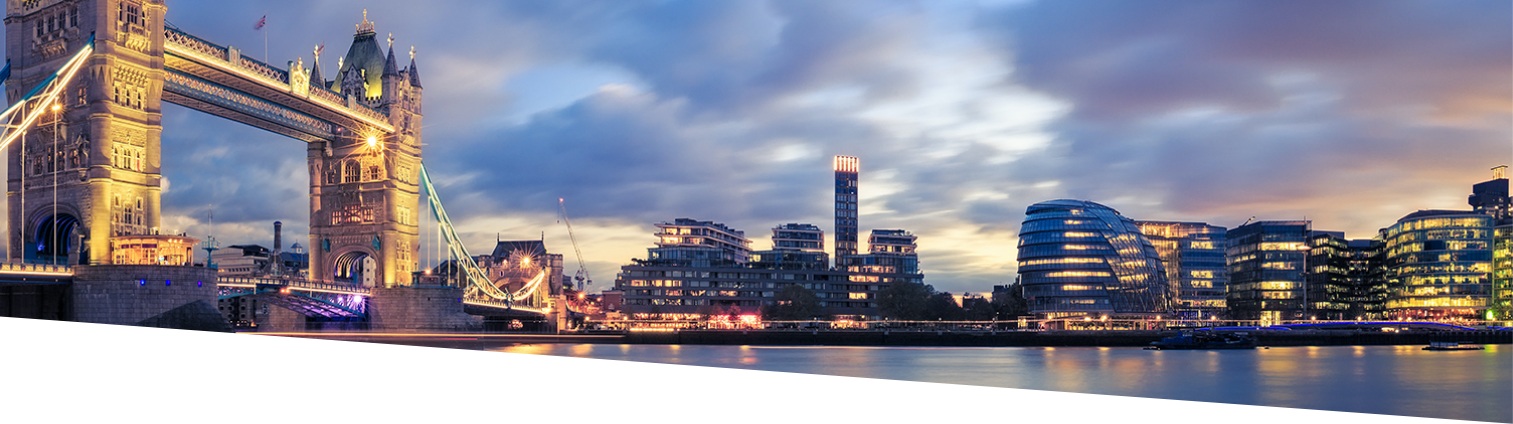
Angle
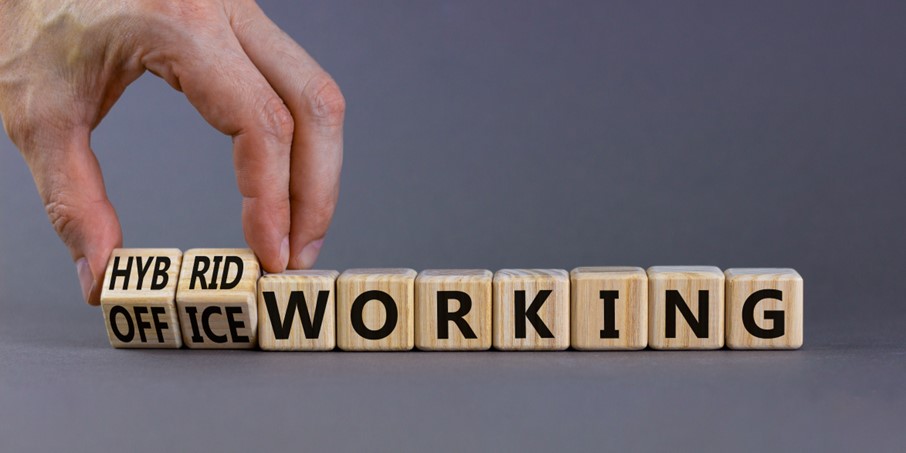
Future Proofing Your Organization: Tips for Optimizing Operations in a Hybrid World
- Business Transformation
- 3 Mins
The adrenaline of the past few years to work remotely and do things differently created a fundamental shift in the way teams work. It turned out that this shift was not a temporary response, but rather a permanent change in the way organizations conduct their business on daily basis. However, the pressure to evolve had been growing for the past decade, with organizations starting to measure key performance indicators around operational efficiencies, cost reduction or avoidance, and productivity – much of which has placed an emphasis on hybrid work.
That’s not necessarily a bad thing: hybrid work can address some of those aforementioned evolving employee needs by allowing a better work-life balance, while also offering some benefits to organizations, such as lower overhead costs and higher employee satisfaction. However, there are undoubtedly some new challenges to address if organizations want to not only keep up with the productivity they enjoyed when their team was in-office full time but exceed it.
If this jarring jump from full time in-office work to fully remote work to hybrid work tells us anything, it’s that the future of business is anything but certain, and while there’s currently no way of predicting what’s to come, there are some ways for companies to adjust their operations and make them more future proof.
Improving Employee Engagement
Devising operational strategies that can continually adapt to an ever-changing business landscape begins with identifying gaps in current processes and pinpointing areas of opportunity. One common area of weakness for modern organizations is in employee engagement.
While some have begun prioritizing the issue, maintaining engaged operational staff continues to be a challenge for many companies today, especially at entry level positions where there is a higher turnover rate. With employee engagement and exit interviews being conducted regularly it is now evident that the lack of engagement and training can push employees in entry level positions to move to jobs that are less monotonous and more rewarding.
According to a study by IBM, employees are 12 times more likely to change jobs if they feel they are not achieving their career goals, and this statistic dramatically increases for new employees to 30 times. The study also revealed that 42% of new employees are more likely to stay at their current jobs when provided with adequate training required to complete tasks.
Maintaining an experienced and familiar staff by providing them with the training, opportunities, and compensation they need to remain engaged and motivated can help organizations maintain the operational stability required to adjust to shifting needs and address emerging challenges.
Developing Strong Standard Operating Procedures
Optimized processes are driven by well-established standard operating procedures (SOPs). Developing strong SOPs can improve efficiency, consistency, and compliance while allowing scalability. SOPs also allow for the cross training of teams, which can help eliminate the siloed approach to office services.
Developing and standardizing effective operational processes can be made easier with the help of key performance indicators (KPIs). Consistently measuring KPIs can help determine a process’s efficacy and provide relevant insights into fluctuations in business, efficiency of workflows, and resource utilization while also helping to create benchmarks for all processes.
Managing Risk
Risk management and mitigation are essential measures to take when optimizing operations, especially in highly regulated industries like banking and finance. It is important to understand that all operational processes have a certain level of risk attached to them and the best approach to assessing risk is to examine each process individually. That can be with the help of various tools, including the following:
Lean Six Sigma
Lean Six Sigma is a methodology used in improving operational processes. It focuses on reducing waste, not only of resources, but of time, energy, and talent. This is done largely by identifying and eliminating redundant, unnecessary, inefficient, and/or defective aspects of operational processes.
Failure Modes and Effects Analysis (FMEA)
FMEA is a structured approach to optimizing operational processes designed to determine the potential failures in a process or procedure. These approaches investigate the potential failures of any process, along with the effects and causes of them. The results from the analysis can support the development of controls to ensure that the risk is mitigated or, on occasion, eliminated altogether.
Establishing a Quality Program
The development of a quality program is critical to ensure the successful optimization of operations at any organization. There are various approaches to setting up a quality program that an organization can take the Total Quality Management (TQM), Lean Six Sigma, ISO 9000 are some examples. Although these processes lean more towards the manufacturing and software industries, they can be excellent starting points for an exceptional and customized quality program.
Emerging Trends in the Optimization of Operations
It’s important for organizations looking to improve their operational processes to keep a close eye on emerging trends. One current trend revolves around digitizing formally manual operations. The pandemic catapulted the shift towards digitization of paper based and manual processes, and the evolution towards a hybrid work environment has pushed organizations to further embrace digitization. This digital transformation reduces costs and errors, increases stability in operations, allows for risk mitigation, and helps reduce governance.
Another emerging trend is the introduction of Generative Artificial Intelligence (GenAI) into various processes. In a recent report, Deloitte stated that the impact of generative artificial intelligence (GenAI) is growing in every aspect of business, with the AI industry projected to exceed $300 million in 2024 and over $700 billion by 2030. From handling routine activities such as generating real time reports and automating operational processes, to undertaking more complex analytics, assessing operational trends and recommendations, GenAI is an operational trend that is optimizing processes and driving profits.
Conclusion
As organizations continue to embrace the shift to hybrid work, they must prioritize essential changes to operations to ensure both a seamless transition and long-term success. It is impossible to predict the future, but understanding the current state of operations, establishing a robust set of SOPs, a resilient quality program, introducing emerging technologies, and enlisting third-party support can help increase the chances of success and optimize operations.
The contents of this article are intended to convey general information only and not to provide legal advice or opinions.